Peningkatan Performa Beton Geopolimer dengan Material Daur Ulang sebagai Solusi Reduksi Emisi Karbon Dioksida
Ditulis oleh Dimas Puji Raharjo
Beton merupakan salah satu material konstruksi yang umum digunakan. Bahan penyusun beton terdiri dari semen, agregat, dan air tetapi masing-masing bahan memiliki kekurangan. Di antara berbagai bahan penyusun, semen mengkonsumsi energi dan emisi gas rumah kaca dengan jumlah besar sehingga menimbulkan dampak negatif bagi lingkungan (Bajpai et al., 2020).
Gambar 1. Grafik emisi karbon dioksida yang berasal dari industri semen global (Statista, 2024).
Menurut projek karbon global, emisi CO2 (karbon dioksida) dari industri semen global cenderung meningkat dalam tiga dekade terakhir. Berdasarkan gambar 1, emisi karbon dioksida yang disumbang industri semen semakin meningkat setiap tahunnya. Sementara itu, negara penyumbang emisi terbesar dari produksi semen adalah Tiongkok, sekitar 750 juta metrik ton pada tahun 2022. Solusi alternatif untuk mengatasi permasalahan tersebut adalah penggunaan material beton yang lebih ramah lingkungan berupa geopolimer.
Kualitas beton geopolimer dapat dioptimalkan melalui peningkatan daya tahan dan nilai permeabilitas ion klorida. Peningkatan daya tahan beton tersebut dapat dilakukan melalui alternatif penambahan jenis material limbah, khususnya pada binder. Selain memperbaiki kualitas daya tahan, pemilihan jenis material limbah yang tepat juga dapat meningkatkan kekuatan dan pengurangan jejak karbon saat proses produksi material penyusun beton. Contoh material binder yang dapat meningkatkan kualitas beton geopolimer adalah limbah konstruksi dan pembongkaran Construction and Demolition Waste (CDW) dengan campuran GGBS atau Granulated Ground Blast-furnace Slug.
Produksi CDW mengalami peningkatan yang signifikan akibat aktivitas konstruksi dan renovasi bangunan yang intensif, pertumbuhan kawasan global dan pembangunan infrastruktur yang semakin pesat (Dündar et al., 2023; Akduman et al., 2023). Hasil yang menjanjikan telah dilaporkan dalam berbagai literatur mengenai CDW sebagai bahan pengikat dalam bahan geopolimer. Oleh karena itu, penerapan material alternatif geopolimer yang berkelanjutan seperti CDW sangat penting untuk keberlanjutan sektor konstruksi dalam jangka panjang. Penambahan GGBS pada material beton geopolimer juga menunjukan hasil positif terkait peningkatan daya tahan beton geopolimer.
Komponen geopolimer selanjutnya yang berperan penting adalah agregat karena mengisi 70% volume beton. Alternatif material agregat dapat berasal dari limbah aktivitas tambang yang berdampak besar pada lingkungan. Limbah dari aktivitas penambangan diperkirakan berjumlah 65 dan 80 miliar ton, sebanyak 10-15 miliar ton diantaranya berupa limbah tailing, dan sisanya berupa batuan. Pengelolaan tersebut masih menimbulkan permasalahan karena mengkontaminasi ekosistem air dan menurunkan kualitas kesehatan masyarakat. Oleh karena itu, limbah tailing emas dimanfaatkan sebagai material agregat beton geopolimer yang tidak menimbulkan permasalahan lainnya.
Isi
Gold mine tailing (MT) dan Construction and Demolition Waste (CDW) atau limbah konstruksi pembongkaran merupakan limbah yang sulit terurai karena mengandung kandungan mineral dan zat yang kompleks. CDW diidentifikasi sebagai sumber aluminosilikat potensial untuk geopolimer. Perpaduan dua komponen ini dapat dijadikan komponen dalam produksi beton geopolimer sebagai alternatif net-zero emission yang ramah lingkungan. Temuan penelitian ini berpotensi mempengaruhi praktik konstruksi berkelanjutan, berkontribusi terhadap pengurangan emisi gas rumah kaca, dan menginspirasi penelitian dan pengembangan lebih lanjut di bidang bahan konstruksi ramah lingkungan.
Bahan CDW dapat berasal dari berbagai limbah konstruksi. Seperti pada gambar 2 yaitu limbah batu bata, limbah ubin, limbah beton, serta limbah kaca. Limbah ini dikumpulkan, dihancurkan, digiling, dan digunakan sebagai sumber aluminosilikat dengan ukuran partikel rata-rata 75 μm. Limbah dihancurkan untuk memperkecil ukuran awalnya menggunakan jaw crusher, yang kemudian digiling dengan ball mill selama waktu konstan 2 jam. Komponen pada ball mill seperti jumlah/ukuran bola yang digunakan serta durasi yang digunakan disesuaikan dengan uji pendahuluan dalam laboratorium. Setelah melalui proses penggilingan, limbah CDW diayak melalui saringan mesh dengan empat ukuran partikel yang berbeda yaitu 225, 150, 75, dan 45 μm yang dipisahkan untuk menilai pengaruh ukuran partikel terhadap kinerja beton. Komposisi kimia yang terkandung pada setiap jenis limbah CDW dapat diukur menggunakan spektrometer fluoresensi sinar-X (XRF).
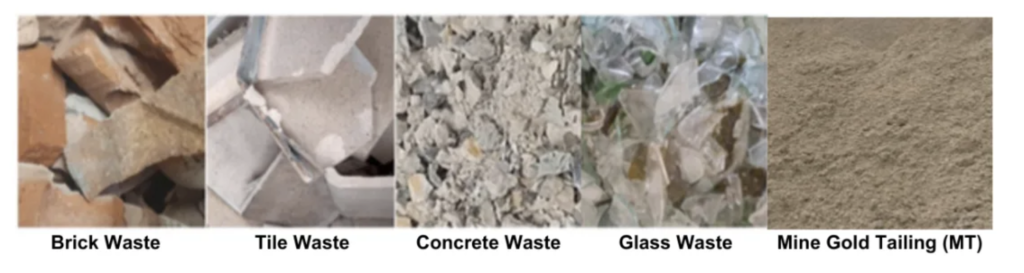
Gambar 2. Bahan Construction and Demolition Waste (CDW) dan Gold Mine Tailing (MT).
Peningkatan daya tahan dari beton geopolimer dapat dilakukan dengan menambahkan GGBS (Granulated Ground Blast-furnace Slag) sebagai campuran dari binder. GGBS merupakan hasil samping dari peleburan bijih besi yang diperoleh melalui pendinginan terak besi cair dari tanur sembur, yang kemudian dikeringkan dan ditumbuk menjadi serbuk. Akan tetapi, campurannya dalam binder beton geopolimer hanya 25% saja, dikarenakan energi yang dibutuhkan untuk produksi GGBS cukup tinggi dibandingkan untuk produksi CDW. Sehingga material CDW memiliki komposisi yang lebih tinggi untuk binder.
Larutan alkali yang digunakan untuk mengaktifkan prekursor adalah NaOH (natrium hidroksida) dan Na2SiO3 (natrium silikat). NaOH disediakan melalui pencampuran antara NaOH dan air, dengan perbandingan yang bervariasi sehingga didapatkan variasi konsentrasi (6-18 M). Sedangkan, Na2SiO3 yang digunakan berbentuk cairan kental transparan yang memiliki kandungan 27,5% SiO2, 64% H2O, dan 8,5% Na2O. Konsentrasi NaOH atau Na2SiO3 secara langsung mempengaruhi reaksi kimia pembentuk matriks geopolimer. Penelitian menunjukkan bahwa Na2SiO3 menghasilkan reaktivitas yang lebih kuat dibandingkan aktivator lainnya, karena partikel silikon mudah terlarut dalam proses geopolimerisasi (Ghafoor et al., 2021).
Pada pembuatan geopolimer ini, ditambahkan pula Gold Mine Tailing (MT) atau tailing tambang emas sebagai agregat. Pada penelitian terdahulu telah menyelidiki bahwa MT dapat digunakan sebagai pengganti semen atau agregat dalam produksi beton karena dapat menjadi material halus yang berukuran lebih kecil dari 200 μm (Pyo et al., 2018). Berdasarkan penelitian yang telah dilakukan, didapatkan karakterisasi fisik MT yaitu berat jenis sebesar 2.75, ukuran partikel rata-rata 0,29 μm, kehalusan sebesar 586,7 m2/kg (Aseniero et al. 2019). Dengan karakteristik tersebut, MT memiliki potensi untuk menurunkan permeabilitas ion klorida dari beton geopolimer. Proses pembuatan beton geopolimer diilustrasikan pada Gambar 3.
Gambar 3. Diagram alir pembuatan beton geopolimer.
Proses pengujian beton geopolimer melalui dua tahap pengujian. Di antaranya adalah pengujian daya tahan dengan uji tekan (compressive test) serta uji permeabilitas ion klorida dengan melakukan uji Rapid Chloride Permeability (RCP). Uji RCP adalah metode uji standar untuk indikasi listrik kemampuan beton dalam menahan penetrasi ion klorida.
Tabel 1. Tabel Hasil Pengujian Rapid Chloride Permeability.
No | Campuran Binder (kg) | Campuran Agregat (kg) | Activator (kg) | Air (kg) | Hasil Uji | Golongan | ||||
FA*1 | GP*2 | Pasir | MT | Kerikil | NaOH | Na2SiO3 | ||||
1 | 340 | 60 | 674 | 0 | 1010 | 52.5 | 105 | 44.5 | 3009 | Medium |
2 | 340 | 60 | 270 | 404 | 1010 | 52.5 | 105 | 44.5 | 1878 | Low |
*1 Fly Ash, *2 Glass Powder
Tabel 1 menjelaskan bahwa campuran kedua dimana terdapat Gold Mine Tailings, memberikan hasil uji yang lebih baik. Total muatan terlewat termasuk dalam golongan rendah menunjukkan bahwa beton tersebut memiliki permeabilitas ion klorida yang rendah. Hal ini menunjukkan bahwa beton geopolimer dengan campuran MT memberikan ketahanan terhadap korosi yang lebih baik daripada beton tanpa campuran MT pada agregatnya.
Konsumsi energi untuk produksi satu meter kubik, baik beton konvensional maupun beton geopolimer bergantung pada komposisi bahan yang terdapat dalam campuran. Gambar 4 menunjukkan estimasi konsumsi energi selama produksi satu meter kubik beton konvensional dan beton geopolimer berbasis CDW. Grafik tersebut didasarkan pada kalkulasi kebutuhan energi untuk setiap bahan. Energi yang diperlukan untuk membuat beton geopolimer berbasis CDW (1,936 GJ/t) lebih hemat 2 MJ/t daripada beton konvensional. Hal ini dipengaruhi oleh OPC menyumbang sekitar 88% dari total energi yang diperlukan untuk produksi beton konvensional (1,71 GJ/t) (Alhalwat et al., 2024).
.
.
Gambar 4. Perbandingan energi produksi (a) beton konvensional (b) beton geopolimer.
Pembuatan setiap material penyusun beton menghasilkan produk samping berupa karbon dioksida. Pada beberapa literatur didapatkan bahwa 0,89 ton CO2 dihasilkan dalam pembuatan satu ton OPC. Hampir 40% emisi karbon berasal dari pembakaran bahan bakar, sedangkan sisanya adalah dekomposisi batu kapur selama proses kalsinasi. Di sisi lain, emisi CO2 terkait agregat, lebih rendah dibandingkan bahan beton lainnya, melepaskan 0,0048 CO2/ton agregat (Alsalman et al., 2021). Gambar 5 menunjukkan bahwa produksi satu meter kubik campuran geopolimer, menghasilkan emisi 40% lebih rendah daripada emisi yang dihasilkan dalam produksi beton konvensional. Hal ini disebabkan oleh adanya OPC yang menyumbang 93% emisi karbon pada beton konvensional. Dengan perbandingan tersebut, beton geopolimer memberikan keuntungan secara ekologis dibandingkan beton konvensional (Alhalwat et al., 2024).
.
.
.
Gambar 5. Perbandingan emisi CO2 (a) beton konvensional (b) beton geopolimer.
Kedua hasil pengujian tersebut memberikan potensi penghematan biaya produksi beton. Penghematan ini diperoleh melalui reduksi energi dan penjualan karbon berdasarkan karbon kredit yang ada. Diasumsikan biaya listrik sebesar Rp1.500/kWh dan rerata produksi beton di Indonesia adalah 10 juta ton/tahun, maka penghematan biaya per tahun yang diperoleh adalah Rp8.325.000.000,-. Berdasarkan CNBC tahun 2023, karbon kredit di Indonesia yang dipatok kementerian Energi dan Sumber Daya Mineral adalah 2 USD hingga 18 USD. Dengan jumlah produksi yang sama maka penghematan biaya yang diperoleh adalah Rp150.101.195.000,- per tahun
Penutup
Salah satu penyebab meningginya emisi gas rumah kaca yaitu berasal dari pembangunan dan kegiatan penambangan. Pembuatan beton geopolimer merupakan salah satu langkah untuk mengatasi permasalahan efek gas rumah kaca yang dihasilkan dan memanfaatkan kembali limbah konstruksi serta penambangan. Peningkatan daya tahan beton dapat dilakukan melalui alternatif penambahan jenis material limbah. Pembuatan beton dengan bahan baku ini dapat mengurangi emisi CO2 yang besar hingga 40%. CDW ditambahkan sebagai binder, sedangkan MT digunakan sebagai agregat. Hasil pengujian memberikan potensi penghematan total mencapai Rp158.426.195.000,- per tahun. Maka dari itu, pembuatan beton geopolimer berbahan dasar limbah daur ulang, dinilai efektif dan dapat berpengaruh dalam upaya pengurangan efek gas rumah kaca.
Referensi
Akduman, S., Aktepe, R., Aldemir, A., Ozcelikci, E., Alam, B., & Sahmaran, M. (2024) “Opportunities and challenges in constructing a demountable precast building using C&D waste-based geopolymer concrete: A case study in Türkiye”, Journal of Cleaner Production, 434, p. 139976. doi: 10.1016/j.jclepro.2023.139976.
Alhawat, M., Yildirim, G., Ashour, A., Ozcelikci, E., Aldemir, A., & Sahmaran, M. (2024) “A study on the influencing parameters in developing construction and demolition waste-based geopolymer concretes and their sustainability assessment”, Construction and Building Materials, 426, p. 136143. doi: 10.1016/j.conbuildmat.2024.136143.
Alsalman, A., Assi, L. N., Kareem, R. S., Carter, K., & Ziehl, P. (2021) “Energy and CO2 emission assessments of alkali-activated concrete and Ordinary Portland Cement concrete: A comparative analysis of different grades of concrete”, Clean Environmental Systems, 3, p. 100047. doi: 10.1016/j.cesys.2021.100047.
Aseniero, E. M., Opiso, M. H. T., & Banda, C. B. (2019) “Potential utilization of artisanal gold-mine tailings as geopolymeric source material: Preliminary investigation”, SN Applied Sciences, 1(1), pp. 1–9. doi: 10.1007/s42452-018-0045-4.
Bajpai, R., Choudhary, K., Srivastava, A., Sangwan, K. S., & Singh, M. (2020) “Environmental impact assessment of fly ash and silica fume based geopolymer concrete”, Journal of Cleaner Production, 254, p. 120147. doi: 10.1016/j.jclepro.2020.120147.
Dündar, B., Tugluca, M. S., Ilcan, H., Sahin, O., & Sahmaran, M. (2023) “The effects of various operational- and materials-oriented parameters on the carbonation performance of low-quality recycled concrete aggregate”, Journal of Building Engineering, 68, p. 106138. doi: 10.1016/j.jobe.2023.106138.
Ghafoor, M. N. S., Khan, Q. S., & Qazi, M. N. (2021) “Influence of alkaline activators on the mechanical properties of fly ash based geopolymer concrete cured at ambient temperature”, Construction and Building Materials, 273.
Pyo, S., Tafesse, B. J., & Kim, H. K. (2018) “Effects of quartz-based mine tailings on characteristics and leaching behavior of ultra-high performance concrete”, Construction and Building Materials, 110–117. doi: 10.1016/j.conbuildmat.2018.01.087.
Statista (2024) “Carbon dioxide emissions worldwide from cement manufacturing from 1970 to 2022”, Statista. Available at: https://www.statista.com/statistics/1299532/carbon-dioxide-emissions-worldwide-cement-manufacturing/ (Diakses pada: 31 Oktober 2024).
.